Deconstruction and the new future of building demolition
- sach285
- Mar 4
- 3 min read
By Sarah Currie-Halpern

After a wrecking ball goes barreling through the walls of a building, what happens to all the building material it rammed through? That’s an increasingly pressing question for waste advocates looking to rethink and ultimately reduce the huge amount of waste produced by construction and demolition (C&D) projects and dumped in landfills across the planet.
Wherever you look, the numbers paint a grim picture. The construction industry produces some 600 million tons of solid waste each year in the U.S., and between 450 and 500 million tons in the E.U., making it the largest waste stream in the European bloc. In the U.K., the construction industry accounts for roughly one-third of the country’s entire waste production and 45% of its carbon emissions; recent building booms in Australia have pushed the country’s C&D waste production to 25 million tons.
In theory, much of this could be prevented. Bulldozing a building means destroying perfectly functional (and therefore reusable) doors, window panes, cabinets, light fixtures, copper pipes, insulation, and wires. Bricks, wood frames, and clay tiles are useless once they’ve been smashed to bits, as are appliances that would otherwise continue to work for years or even decades. Broadly speaking, the solution is simple: don’t destroy these things. Take them apart and use them in new buildings.
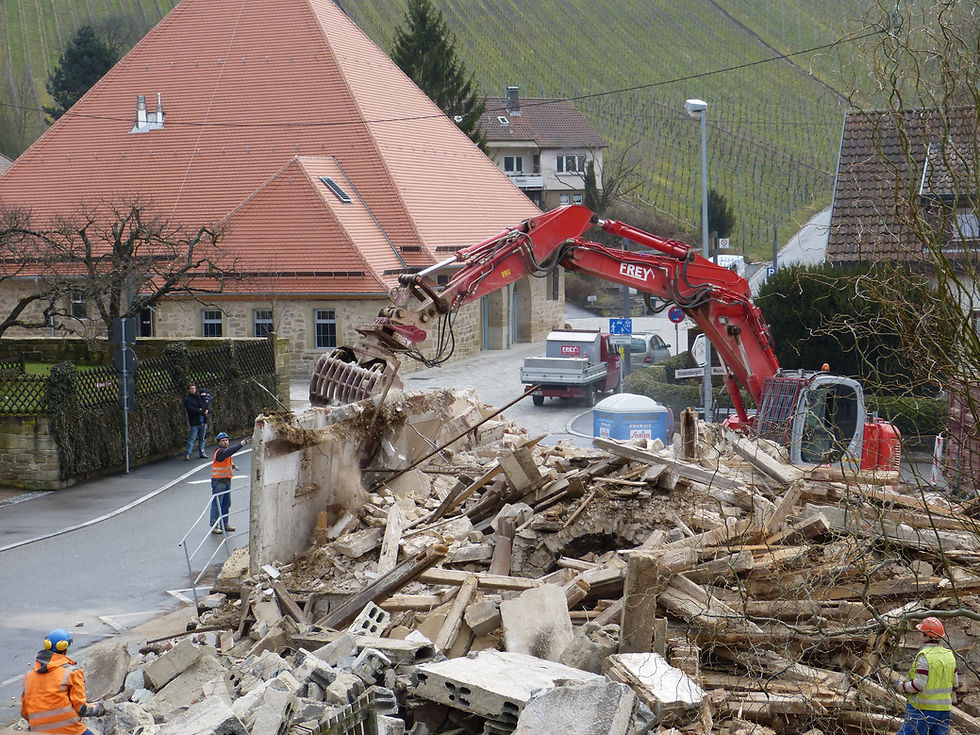
Thanks to a growing number of local ordinances, that’s starting to happen. Local governments in Pittsburgh, San Jose, and Boulder have passed legislation requiring sustainable deconstruction measures for certain projects. Independent sustainable deconstruction companies have cropped up across the U.S. and Canada: BlueEarth in Illinois, Perks Deconstruction in Colorado, Ouroboros Deconstruction in Ontario, and Sledge in Washington. Many of these companies earn revenue by reselling salvaged material, from brass knobs and bathroom mirrors to entire loads of lumber. Also powering this circular economy are businesses that apply a thrift store model to building supplies, accepting donations of construction materials and then reselling them at a discount.
While diverting C&D waste from the landfill by the ton is a noble pursuit in and of itself, the success and spread of deconstruction also depends on making it desirable from a financial standpoint. In other words, the time and cost of sustainable deconstruction is arguably the biggest hurdle to widespread adoption. Wrecking balls are faster and cheaper, and don’t involve an appointment with an appraiser going through the building to see what can be salvaged and for how much. Donations to construction salvage thrift stores, including Resource Central in Boulder, are tax deductible, but that on its own is not enough.
This is where larger, more ambitious incentives would be helpful. That’s starting to happen too. In 2019, the Dutch government approved a number of tax benefits for construction companies that implement circular practices such as creating “material passports,” digital documents containing detailed information on the toxicity, reusability, origin, and value of all the materials in individual buildings. The kind of data material passports contain could be nothing short of instrumental in encouraging deconstruction and diverting construction waste, especially when paired with adequate tax incentives.
Deconstruction has the potential to shrink the biggest waste stream in the world if (and only if) it goes mainstream. This will require both investment in the resources essential to the process and serious political will, primarily in the form of ordinances and economic incentives. Awareness and advocacy efforts are now as crucial to this effort as supporting entrepreneurs and companies in the sustainable C&D space. In other words, deconstruction has a promising future, but whether or not its potential is realized will ultimately be decided in the halls of power, not on the worksite.
Comentarios